Design philosophy
Filter medium is made of compressed Wire Mesh Permeable Material (WMPM).The
WMPM material manufactured by cold plastic deformation (no welding or
brazing). This creates a wire mesh whose porous system is "open in all
directions" and provides the required mechanical, physical, and
hydrodynamic parameters, unlike the traditional wedge wire filters.
This design feature results in large working filtration surface area in
small volume which reduces size of the unit and significantly increases
time between cleaning cycles. Only several external layers utilized
during filtration for the filter element design for back wash operation
(not a volumetric filter).
|
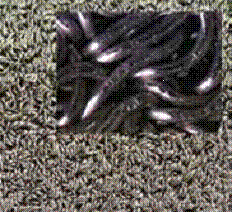 |
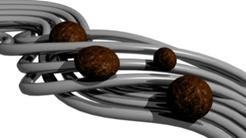 |
Wire mesh is structured to create crescent shaped slots, so particle can
travel along slot till s top
without being pressed and locked between wires. This minimizes particle
obstruction, prevents filter cake formation and helps during back wash
cleaning. The coils of wire of the WMPM filter form a lattice and are
not fixed, so the coils can move relative to each other, displacing
particles and letting them loose. |
The
filter element structure is flexible and elastic and allows shrinkage of the
slots during filtration and expansion of the slots during cleaning which
improves quality of filtration and regeneration of the filter to original
condition after back flushing. Differential pressure across filtering element
created during cleaning cycle causes the filter elements to expand (elasticity
of WMPM), release particles and regenerate the filter.
Filter elements assembly can be designed to utilize differential pressure
across filter to compress and expand filtering element not only in radial
direction, but also axially which will provide additional increase in
performance and regeneration.
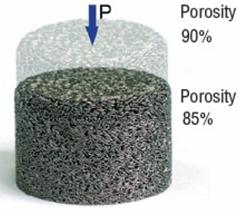
The essential WMPM feature is its elastic deformation properties, which
allowchanges in porosity by varying the pressure load as shown in the pressure
(P) vs.Porosity (S) in Figure 15. During filtration operation (pressure from
outside to inside)the element porosity reduces, enhancing filtration efficiency
and during leaningoperation (pressure from inside to outside) the porosity
increases, improving theremoval of captured particles and causing effective mesh
regeneration. The elasticproperties of the WMPM filter elements result in a low
sensitivity to mechanical andthermal shock
Cleaning and Back Washing
The filter element structure is flexible and elastic and allows shrinkage of the
slots during filtration and expansion of the slots during cleaning which
improves quality of filtration and regeneration of the filter to original
condition after back flushing. Differential pressure across filtering element
created during cleaning cycle causes the filter elements to expand (elasticity
of WMPM), release particles and regenerate the filter. Low flow rates for back
flushing can be used due to expansion of the slots and release of the particles.
The cleaning operation is reverse flow at the same flow rate as filtration flow
rate. The filter doesn't require any internal moving parts like suction scanners
or filter candle selector valves. Thus it reduces the failures caused by
mechanical components wear and fatigue over time, resulting in high reliability.
Back flushing does not affect the degradation of filter elements over time, so
the lifeof filter elements is not limited by number of cycles. Longer filtering
operationsbetween cleaning cycles reduce total number of cycles required during
design life.
Material
The initial material for compressed wire mesh filters is metal wire of the
required grade (Grade of the material is selected for application) and diameter
(0.03–2.5 mm).
-
Stainless steel
-
Duplex and Super Duplex steel
-
Inconel
-
Monel
-
Others
Shape
Filter element can be designed and formed in variety of shapes to fit desired
housing and meet application requirements.
Design Considerations
For applications with flow rates from 10 GPM to 20,000 BPD the single filtration
unit is provided. Filtration candles assembled from standard cylindrical
filtration element are placed in the filtration unit. Quantity of the candles is
selected to support required flow rate and duration between cleaning.
The filtration unit casing can be provided with customer specified inlet/outlet
connections and additional instrumentation. Back washable units are provided
with all equipment required for automated filtration and cleaning cycles.
|
|
Filtration quality |
from 30 μm to 600 μm |
Process temperature |
from - 76°F to + 1500 °F |
Max. Δp across filter element |
up to 360 PSI |
Max. Allowable Working Pressure |
up to 29,000 PSI |
Applications
-
High temperature applications
-
Corrosive fluids and gases
-
Mechanical and thermal shock; vibration
-
Mechanical and hydraulic impact on filter element
-
Spikes in flow rates, pressure and contaminant properties
-
Increased duration between replacement or cleaning
-
Limited space
Industries
-
Oil and gas industry
-
Automotive
-
Mining
-
Power Generation
-
Aero and space
-
Shipbuilding, ballast water filtration
-
Railway transport
-
Sea water filtration
-
Municipal
|